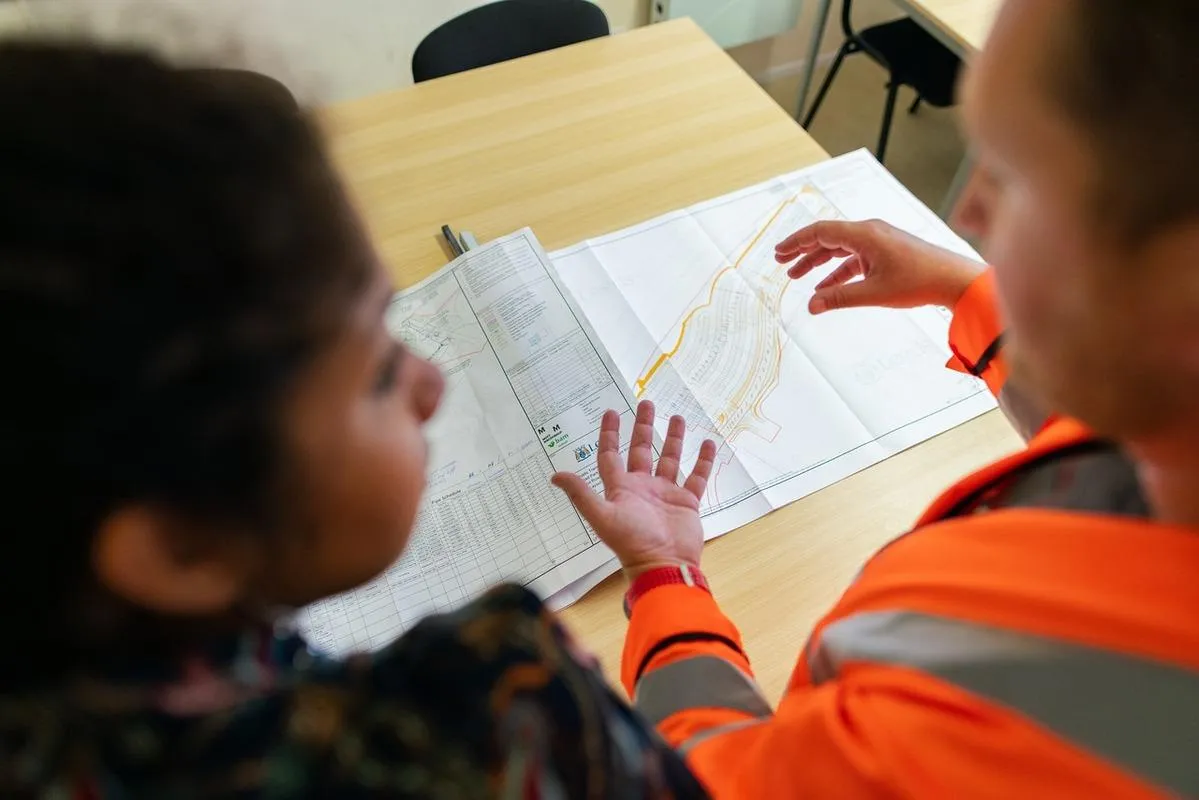
Lean Manufacturing Engineer: 2025 Job Overview
The industrial world's buzzing, and right in the thick of it are Lean Manufacturing Engineers – the people shaping how things get made.
With data smarts and lean thinking now table stakes for staying ahead, the need for these skilled pros is seriously taking off.
So, what exactly does a Lean Manufacturing Engineer do in 2025? Let's dive into their role, the current hiring scene, and what they earn.
What is a Lean Manufacturing Engineer?
So, what exactly is a Lean Manufacturing Engineer? They are the specialists we rely on to strategically minimize waste, optimize our production workflows, and ultimately enhance the overall efficiency of our manufacturing environment. They leverage established lean methodologies, such as Six Sigma, Kaizen, and Value Stream Mapping, to facilitate our processes and achieve significant cost reductions while maintaining our rigorous quality standards.
Where they truly stand apart is in their integration of continuous improvement strategies and robust data analytics into daily operations.
Lean Manufacturing Engineer Job Description
So, when you look at what a Lean Manufacturing Engineer does these days, it's usually a mix of getting down in the weeds technically, thinking analytically, and knowing how to manage processes like a pro. Their typical day-to-day often includes things like:
Timing how things are done on the floor to spot any wasted steps.
Putting lean principles into action – think things like 5S for organization, Kanban for managing flow, and JIT for keeping inventory lean.
Keeping an eye on the numbers – developing and digging into key performance indicators (KPIs) to see how things are really running.
Getting different teams working together to make things better, constantly.
Using data on how efficient processes are to make smart calls about what to do next.
Making sure everything we're doing ticks all the boxes for regulations and quality.
Teaming up with the automation and data science folks to figure out how to make workflows even smoother.
Lean Manufacturing Engineer Salary Trends in 2025
Looking at 2025, you'll typically see Lean Manufacturing Engineers in the US earning somewhere between $80,000 and $110,000 a year.
Of course, that can shift depending on how much experience they've got under their belt, the specific industry they're in, and where they're located. If someone's got deep knowledge in areas like automation, data analytics, or knows the ins and outs of regulations for a particular industry, they can often expect to see even higher paychecks.
In high-demand areas like automotive, aerospace, and electronics manufacturing, salaries may exceed $120,000.
Lean Manufacturing Engineer Recruitment Trends
Now, it's not just about having that solid engineering background; employers are really keen on people who understand things like smart manufacturing, how the Internet of Things fits into production, and making decisions based on data.
When recruiters are looking, they're really focusing on:
Can you actually show you've used lean methods and made a difference?
Are you good at working with different teams, maybe even teams with people from different backgrounds?
Do you understand the data that helps you make lean production even better?
Can you communicate clearly and take charge when necessary?
Looking at what employers are after in 2025, there's a big trend towards wanting people with a mix of skills – someone who knows their engineering but can also handle data and is comfortable with software. That combination is becoming really valuable.
Lean Manufacturing Engineer Hiring Best Practices
To really snag and keep those top-notch lean engineers, companies need to sharpen their hiring game. Here are some smart moves for finding Lean Manufacturing Engineers in 2025:
Show them the path ahead: Lean engineers are all about getting better, so highlight opportunities for training and chances to lead projects that actually make a big impact.
Talk about the data: These folks are often into modern tools, like when you use predictive analytics and machine learning to make lean processes even better. Make sure to mention those kinds of initiatives.
Shout about being green and innovative: Engineers today often want to work on making things more sustainable and coming up with new, better ways of doing things. If your company's doing that, make it known.
Point out the teamwork: Being able to work with different teams – like the folks in logistics or the IT department – is a big draw. Let candidates know they'll get to collaborate across the company.
Also, teaming up with recruitment companies that really know the lean manufacturing world can make the whole hiring process smoother and help you find people who are the right fit.
Partner With Talent Traction
At Talent Traction, we specialise in connecting manufacturing businesses with top-tier Lean Manufacturing Engineers who bring a rare mix of technical ability, data fluency, and process improvement experience.
Whether you need contract support, a permanent hire, or strategic guidance on building lean capability across your teams, our recruitment experts are here to help.
FAQs
What qualifications should we look for in a Lean Manufacturing Engineer candidate?
Ideally, candidates should have a degree in industrial or mechanical engineering and hands-on experience with lean tools like Six Sigma, Kaizen, or Value Stream Mapping. Certifications such as Lean Six Sigma (Green or Black Belt) are strong indicators of expertise.
Is hiring for lean roles still relevant in today’s data-driven manufacturing environment?
Yes—more than ever. Lean thinking is evolving with digital transformation. The best candidates today blend traditional lean methodologies with data analysis and tech fluency, making them essential for staying competitive in 2025.
Which industries are most competitive when hiring Lean Manufacturing Engineers?
Sectors like automotive, aerospace, and high-tech electronics are extremely competitive. If you're hiring in these areas, you’ll likely need to move fast and offer clear growth opportunities to secure top talent.
How important is data analytics experience for lean-focused roles?
Crucial. Modern lean engineers need to work with performance metrics, interpret production data, and support predictive decision-making. Candidates who understand automation tools, ERP systems, and analytics platforms bring a huge advantage.
What soft skills should we prioritize when screening candidates?
Strong communication, cross-functional collaboration, and leadership skills are key. Many lean projects involve working across departments, so the ability to influence others and drive change is just as important as technical know-how.
Are there hiring models that work best for lean engineering roles?
A blended hiring strategy works well. Contract or interim hires are great for project-based lean initiatives, while direct hires are better for long-term process transformation roles. Upskilling internal teams can also complement external hires.
What hiring challenges should we anticipate when recruiting Lean Engineers?
The biggest challenge is finding candidates who check all the boxes: lean expertise, data literacy, and team leadership. Many engineers are strong in one or two areas but not all three. That’s why partnering with a specialist recruiter is often essential.
How can Talent Traction support our lean hiring needs?
Talent Traction specialises in recruitment for the manufacturing, automotive, and construction sectors. We understand what makes a top-tier Lean Manufacturing Engineer and can connect you with pre-vetted candidates who fit your culture, project goals, and technical requirements.
Facebook
LinkedIn
Youtube
Instagram