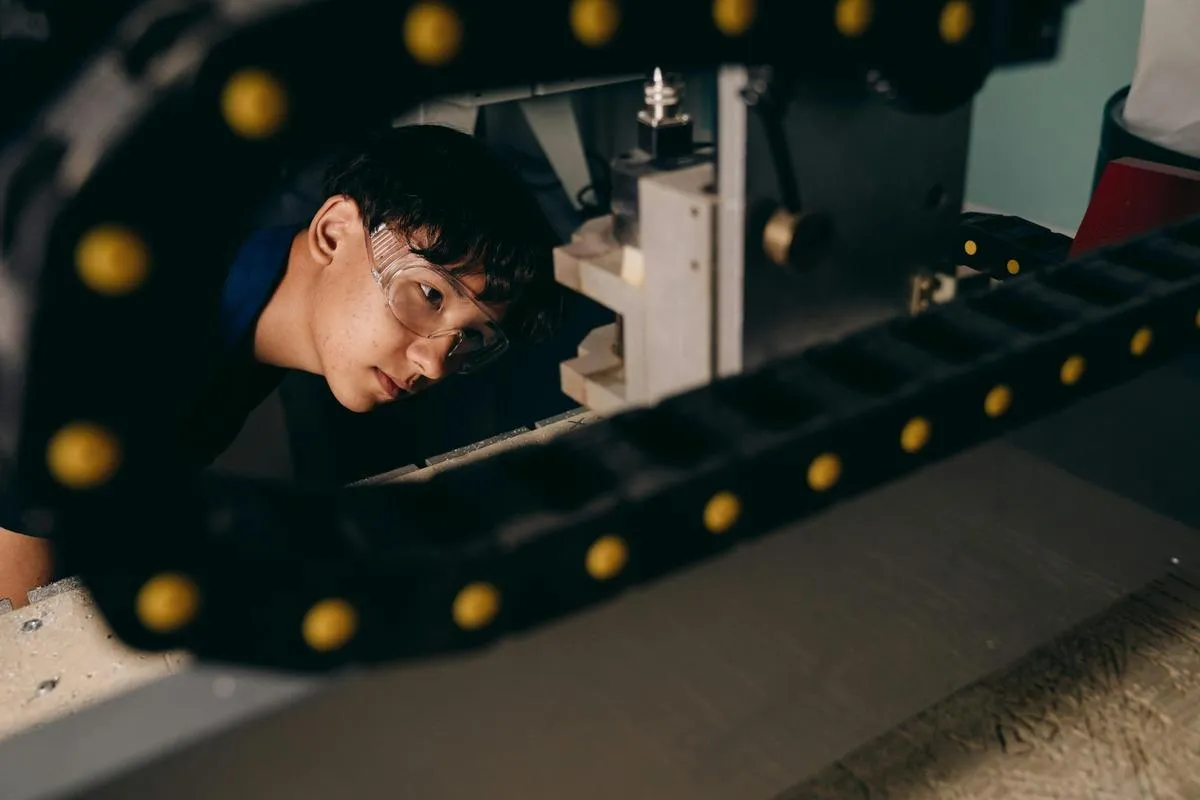
Industrial Engineer: 2025 Job Overview
In 2025, Industrial Engineers are the unsung heroes of efficiency, scalability, and sustainability, steering businesses through an ever-changing world.
They’ve outgrown their old role of fine-tuning factory floors and now harness technology, data analytics, and lean principles to overhaul operations across industries like manufacturing, automotive, construction, and logistics. Hiring the right Industrial Engineer isn’t just a smart move—it’s a game-changer, delivering cost savings, ramped-up productivity, and a business ready for tomorrow’s challenges.
This guide cuts straight to the point: what Industrial Engineers do in today’s world, how much they’re paid, what qualities to hunt for in candidates, and how to land the best talent in a tough market.
What is an Industrial Engineer?
Industrial Engineers are the go-to experts for designing and improving systems that connect people, machines, materials, and information. Their big goal is to make things run smoother, save money, and grow easier. In 2025, they use a bunch of cool tools and tricks to get it done:
Lean Six Sigma: A smart way to ditch waste and keep things efficient.
Smart Manufacturing Technologies: High-tech automation to keep processes flowing.
Data Analytics and Simulation Software: Handy tools to dig into data and test ideas for better results.
Sustainability Metrics: Guides to keep things green and in line with eco-friendly goals.
Cross-Functional Collaboration: Teamwork strategies to make the most of everyone’s skills across departments.
As systems thinkers, Industrial Engineers keep everything humming along, whether it’s a factory floor or a supply chain. Their know-how boosts performance and backs up sustainable ways of working, making them a key part of today’s industries.
Industrial Engineer Job Description (2025 Edition)
A modern industrial engineer job description should include a mix of engineering knowledge, project leadership, and data-driven problem-solving. Key responsibilities include:
Analyzing existing production and workflow systems to identify inefficiencies and bottlenecks
Developing and implementing process improvements across operations
Designing layouts for new facilities or optimizing existing ones for better output
Conducting time studies and capacity analyses
Collaborating with departments such as quality, maintenance, and logistics
Integrating automation, robotics, or IoT solutions into production environments
Using analytics platforms and simulation tools to evaluate proposed changes
Monitoring KPIs and continuous improvement metrics
In 2025, the best Industrial Engineers combine hands-on problem solving with digital fluency.
Industrial Engineer Salary in 2025
As a hiring manager, determining the right salary for an industrial engineer in 2025 is a critical step to secure top talent in a competitive market. The average industrial engineer in the U.S. earns between $80,000 and $110,000 per year, but for senior professionals with niche expertise—think digital manufacturing, sustainability, or automation—you’re looking at $120,000 or higher, especially in high-stakes industries like aerospace, automotive, or pharmaceuticals.
To craft a compelling offer, focus on several key considerations that reflect both the candidate’s worth and my organization’s needs. Here’s what I weigh when setting a salary:
Experience: A candidate with a solid history in my sector or a related field brings immediate value; be prepared to pay more for that expertise.
Certifications: Credentials like Lean Six Sigma or PMP aren’t just buzzwords—they signal a level of mastery that can justify a higher salary.
Technical Skills: Proficiency in tools like AutoCAD, SolidWorks, MATLAB, or Python is a must in today’s tech-driven world.
Systems Knowledge: Familiarity with ERP, MES, or simulation software shows they can hit the ground running, which is worth a premium.
Leadership Potential: If they’ve led teams or managed projects, they’re bringing more to the table, so adjust the compensation to reflect that.
Industrial Engineer Recruitment Trends in 2025
Recruiting Industrial Engineers in 2025 means navigating a competitive market where demand outpaces supply. Here’s what hiring managers need to know:
1. Tech Integration is Non-Negotiable
Engineers with experience in automation, data systems, or smart factory tools are top of the list.
2. Soft Skills Are a Deal-Breaker
The ability to communicate across teams, present findings, and lead change management initiatives is just as important as technical skills.
3. Project-Based Hiring Is Growing
Many companies are bringing in Industrial Engineers for transformation initiatives, such as lean implementation, plant redesigns, or system upgrades.
4. Cross-Functional Experience Adds Value
Engineers who have worked across supply chain, quality, and production are more adaptable and impact-ready.
The Role of Data and Digital Tools in 2025
The role of the Industrial Engineer has gone digital. Today’s professionals are expected to leverage real-time data, simulations, and analytics platforms to guide operational decisions.
Tools they commonly use:
Power BI and Tableau: These are your go-to for whipping up performance dashboards. Think of them as a window into what’s happening on the floor, updated live.
AutoCAD and simulation software: Perfect for designing and modeling facilities or workflows—like a digital sandbox to test ideas before they go live.
Python or R: These are the heavy hitters for statistical analysis, letting engineers dig into data and spot trends that others might miss.
ERP and MES platforms: These keep everything connected, integrating data across systems so nothing slips through the cracks.
Digital twins: Imagine a virtual clone of your operations. Engineers use these to simulate process changes and see what works—without touching the real world yet.
Now, when you’re sizing up candidates, don’t just check if they’ve heard of these tools. You want someone who can extract insights from data and turn them into meaningful improvements. Look for folks who can show you real examples—maybe they’ve boosted efficiency or cut downtime using these skills. That’s the gold standard.
Continuous Improvement Metrics for Industrial Engineers
A strong Industrial Engineer doesn’t just build better systems—they measure and prove the results. In 2025, commonly used continuous improvement metrics include:
Cycle time and lead time
Overall Equipment Effectiveness (OEE)
First-pass yield (FPY)
Capacity utilization rates
Cost per unit produced
Carbon footprint and energy efficiency metrics
Employee productivity and ergonomics data
Look for candidates who have successfully driven change in one or more of these areas.
Industrial Engineering Staffing Solutions
To keep up with project demands, automation rollouts, or facility expansions, more companies are relying on industrial engineering staffing solutions. These include:
Contract and interim engineers for project-based or seasonal work
Direct hire support for building in-house engineering teams
Consultants to lead lean, Six Sigma, or automation initiatives
Rapid sourcing for roles in remote or hard-to-hire areas
Onboarding assistance for smoother integration and ramp-up
Working with a recruitment partner that understands engineering saves time, cuts costs, and improves hiring quality.
Partner With Talent Traction
At Talent Traction, we specialise in recruiting top-tier Industrial Engineers for manufacturing, automotive, construction, and logistics companies.
Our deep industry knowledge means we don’t just look at resumes; we look at how well someone can perform, grow, and fit into your team’s vibe. Whether you’re scaling up your operations, trying to make things more efficient with lean initiatives, or automating your production lines, we’ve got your back with the right engineer for the job.
Here’s what we bring to the table:
Staffing options that work for you: We offer permanent, contract, and interim placements—whatever suits your needs.
Pre-screened pros: We’ll hook you up with a shortlist of candidates who already know the ins and outs of your industry.
Nailing those tricky roles: We run targeted campaigns to track down talent for those hard-to-fill, niche spots.
Fast, but spot-on: We move quickly to find you the perfect fit without skimping on quality.
FAQs
1. What does an Industrial Engineer do in 2025?
They design and improve systems for production, logistics, and operations—using data, automation, and lean principles to increase efficiency and reduce cost across the organization.
2. What should we include in an industrial engineer job description?
Highlight technical expertise (e.g., lean, Six Sigma, AutoCAD, ERP systems), data fluency, cross-department collaboration, and experience with process optimization.
3. What’s the typical salary for an Industrial Engineer in 2025?
The average salary ranges from $80,000 to $110,000, with higher pay for specialists in smart manufacturing, automation, or leadership roles.
4. What certifications are valuable for Industrial Engineers?
Lean Six Sigma (Green or Black Belt), PMP, and certifications in simulation or automation tools (e.g., Siemens, Autodesk) are highly valued.
5. What industries are hiring the most Industrial Engineers?
Manufacturing, automotive, aerospace, logistics, and construction sectors are leading demand—especially as they modernize operations and adopt Industry 4.0 solutions.
6. How has the role evolved in recent years?
Today’s engineers are expected to use data analytics and digital tools to guide decisions, not just fix processes. The role is more strategic, collaborative, and tech-centric than ever.
7. Should we hire full-time engineers or use staffing solutions?
Use full-time hires for ongoing needs, and engineering staffing solutions for transformation projects, plant expansions, or temporary process improvements. A blended model often works best.
8. How can Talent Traction support our industrial engineer recruitment?
We provide access to vetted, qualified candidates who bring both technical and leadership capabilities. Whether you need a contract engineer or a long-term team member, we help you hire fast and with confidence.
Facebook
LinkedIn
Youtube
Instagram